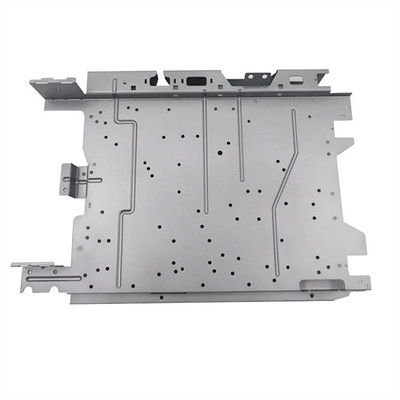
CNC Punching
CNC Punching is a highly precise and efficient metal fabrication process that uses computer numerical control (CNC) technology to punch holes, shapes, or patterns into metal sheets. This process is widely used in manufacturing due to its ability to produce complex designs with high accuracy and repeatability. CNC punching machines are equipped with programmable tools that can perform a variety of operations, such as cutting, forming, and embossing, making them versatile for a wide range of applications.
CNC Punching is an advanced processing method that combines computer numerical control (CNC) technology and stamping machining. CNC technology achieves the machining of the desired shape by precisely controlling the movement of the machine tool and the operation of the tool. In stamping, this technology makes the operation of punching presses and dies more precise and efficient.
The advantages of CNC Punching:
1. High precision: CNC Punching can accurately control the depth, position and speed of stamping to ensure that the processed parts have extremely high dimensional accuracy. This makes CNC stamping ideal for manufacturing complex-shaped parts that require high precision.
2. High efficiency: CNC Punching relies on precise molds and advanced CNC technology, which can achieve high-speed and continuous stamping operations and significantly improve production efficiency.
3. High degree of automation: CNC Punching technology reduces human intervention, reduces the possibility of human error, reduces downtime, and further improves processing efficiency.
4. Save mold costs: CNC Punching is suitable for large products, if large products are stamped with ordinary stamping, huge mold costs are required, CNC Punching can greatly save mold costs through the combination of multiple small molds.
CNC Punching is widely used in various industries, such as aerospace, automobile manufacturing, medical equipment, electronic equipment, etc., to manufacture parts of various complex shapes, including precision parts and large structural parts.
However, there are also some challenges and limitations associated with CNC Punching. For example, CNC machine tools are expensive to purchase and maintain, and require professional technicians to maintain them. In addition, CNC machining has high requirements for operators, requiring certain programming and machine operation skills. For operators with no relevant experience, it may take time and effort to learn and master these skills.
Applications of CNC Punching
Electrical Appliances
In the electrical appliances industry, CNC punching is used to manufacture components such as control panels, brackets, enclosures, and heat sinks. These parts require precise dimensions and durability to ensure the proper functioning and longevity of appliances like refrigerators, washing machines, and air conditioners.
Control Panels: CNC punching creates precise cutouts for buttons, displays, and ventilation holes.
Brackets and Mounts: These components are often produced with high accuracy to ensure proper assembly and stability.
Enclosures: CNC punching is used to create durable and aesthetically pleasing housings for electrical components.
LED Lighting
CNC punching plays a critical role in the LED lighting industry by producing components such as heat sinks, reflectors, and mounting brackets. These parts require precise designs to optimize light distribution, heat dissipation, and overall performance.
Heat Sinks: CNC punching creates intricate patterns and perforations in heat sinks to improve thermal management.
Reflectors: Precise punching ensures accurate light reflection and distribution in LED fixtures.
Mounting Brackets: These components are often customized to fit specific lighting designs and installations.
Packaging
In the packaging industry, CNC punching is used to manufacture metal containers, lids, and decorative elements. The process is ideal for creating perforated designs, ventilation holes, and custom shapes for packaging solutions.
Metal Cans and Containers: CNC punching is used to create precise openings, handles, and decorative patterns.
Lids and Closures: Punching ensures airtight seals and easy-open features for packaging.
Decorative Elements: CNC punching can produce intricate designs for branding and aesthetic purposes.
Construction
In the construction industry, CNC punching is used to produce structural components, cladding, and architectural elements. The process is ideal for creating durable and precise parts that meet the demanding requirements of construction projects.
Structural Components: CNC punching is used to create beams, brackets, and supports with high precision.
Cladding and Panels: Punching ensures accurate cutouts for ventilation, lighting, and aesthetic designs.
Architectural Elements: CNC punching can produce decorative metalwork for facades, railings, and interior designs.
CNC Punching is a versatile and efficient manufacturing process that plays a vital role in industries such as electrical appliances, LED lighting, packaging, and construction. Its precision, speed, and flexibility make it an ideal choice for producing high-quality components with complex designs. As a manufacturer, leveraging CNC punching technology can help you meet the diverse needs of your clients while maintaining high standards of quality and efficiency.